Introduction of
Knife Grinding Machine
Blade Grinding Machine is Known with a few names like , Knife Grinding Machine, Edge Grinding Machine, Surface cum Edge Grinding Machine, Knife Sharpening Machine, Blade Sharpening Machines.
All Machines are comparative with little changes, Knife Grinding Machine are proficient to granulating on edges, knifes to make it more keen with certail points according to client requirement.Blade Grinding Machines gave two variations , one is bunching framework and other is Magnetic Chuck System
Sharp edges are fitted on the table with amassing or attractive hurl framework, attractive toss holds the blades, edges firmly for pounding the edges.Machine table can do granulating in the middle of o to 90 degrees point.
• Complete with electrical and electric engines
• Two no. of 3 stage engines
• One Coolant Pump and other electrical are standard make
• Smooth inward region for great cooling, water waste and simple cleaning
• Grinding head accessible with 6 or 8 crushing stones or according to prerequisites Application Areas.
• Used for honing guillotine paper cutting blades
Overview
Knife Granulating Machine furnished with Complete electrical and electric engines , 2nos. of 3 stage engines ,Coolant Pump framework , fine inner bits for great cooling, water waste and simple cleaning , Grinding head accessible with 6 to 8 granulating stones , Knife honing machine is use for honing guillotine paper cutting blades.
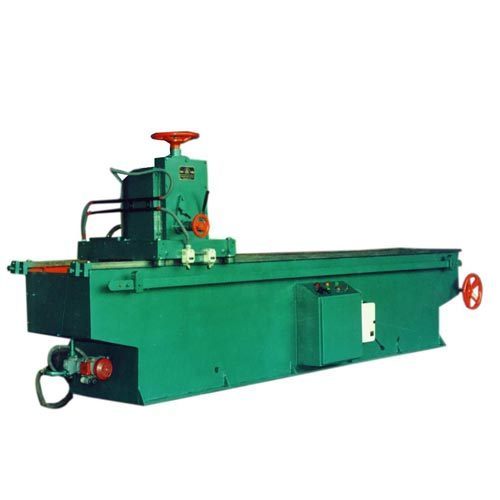
The more modest the point between the edge and stone, the more keen the blade will be, yet the less side power is expected to twist the edge over or break it off. The point between the cutting edge and the stone is the edge point – the point from the vertical to one of the blade edges, and equivalents the point at which the edge is held. The all out point from one side to the next is known as the included point – on a symmetric twofold ground edge (a wedge shape), the point from one edge to the next is along these lines double the edge point. Average edge points are about 20° (making the included point 40° on a twofold ground edge).[1] The edge plot for sharp blades can be just 10 degrees (for a 20° included point). Blades that require an intense edge (like those that cleave) may hone at 25° or more.
Various blades are honed diversely as indicated by crush (edge calculation) and application. For instance, careful surgical blades are incredibly sharp however delicate and are by and large discarded, instead of honed, after use. Straight razors utilized for shaving should cut with insignificant pressing factor, and subsequently should be exceptionally sharp with a little point and frequently an empty crush. Ordinarily, these are honed every day or all the more regularly. Kitchen blades are less sharp, and for the most part cut by cutting instead of simply squeezing, and are prepared day by day. At the other limit, a hatchet for slashing wood will be less sharp still, and is essentially used to part wood by hacking, not by cutting, and might be reground but rather won’t be honed day by day. As a rule, yet not generally, the harder the material to be cut, the higher (more blunt) the point of the edge.
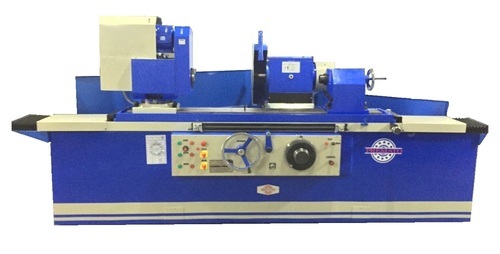
The piece of the stone influences the sharpness of the edge (a better grain, typically, however not generally, produces more honed cutting edges), as does the creation of the edge (a few metals take and keep an edge better compared to other people). For instance, Western kitchen blades are normally made of gentler steel and take an edge point of 20–22°, while East Asian kitchen blades are customary of harder steel and take an edge point of 15–18°. The Western-style kitchen blades are for the most part in the scope of 52–58 on the Rockwell scale, which means the general hardness of a material.
Esskay lathe manufacturers is one of the most reputed manufacturers and dealers of quality lathe machines, CNC, grinding machine, Shaper machine, Surface machine, drilling machines, milling machines, hydraulic brake etc. we are the best radial drilling machine manufacturer, slotting machine manufacturers in Punjab, slotting machine manufacturers in Punjab and shaping machine manufacturer in India.